BLENDAIRE II PACKAGED LPG-AIR MIXING SYSTEM
​
The STATE OF THE ART mixing system
BLENDAIRE II LPG/AIR MIXERS
BLENDAIRE II uses a proprietary control system housed in a SIEMENS PLC for mixing gases in parallel streams. It revolutionizes the conventional passive way of correcting the mixing ratio in a typical mixer. Typically, a correction occurs only when deviation from a setpoint is detected. That is too late! We PREVENT the error from occurring! BLENDARIRE II is a versatile gas mixing system for LPG and air mixing, manufactured gas or natural gas conditioning with LPG (for CV enrichment) or air (for dilution). It replaces conventional piston mixing systems and provides many additional advantages. Typically, there is also a cost savings. This is only possible with our advanced and proven state-of-the-art control technology. The concept of parallel-stream mixing is a premium grade mixing solution, required when stringent requirements are to be achieved. For example, when very accurate CV control is required for an industrial process, or there are changes in the quality of the feedstock.
​
LPG vapor at regulated pressure is sent through a flow meter and next enters the mixing section of the BLENDAIRE II. Here it mixes with compressed air, which is injected at a rate controlled by the airflow control valve. The compressed air is regulated to a pressure above the LPG pressure; the mixed gas (SNG) pressure is the same pressure as the LPG pressure. The flow of LPG is automatically controlled by the upstream regulator at a rate required to meet the current SNG demand. This signal is sent to the PLC where it is converted into standard flowrate using the pressure and temperature information from the transmitters located near the flow meter. The PLC also calculates the necessary actual flow rate of air to achieve the required mixing ratio, again, based on the measured line pressure and temperature and assumed CV value of LPG. The control system issues commands to adjust the air flow control valve to a position to allow this flow rate necessary to pass through. Since the air flow control valve responds o changes in LPG flowrate before the two gases mix, it is a feed forward control system as opposed to conventional feedback systems. The latter style system only responds to mixing errors found by the downstream monitoring instrument, for example, a calorimeter. Any correction occurs minutes after the wrong mix has been generated. Such lag time in conventional mixers causes control oscillation and results in unstable outputs. The BLENDAIRE II makes great improvement on this due to its feed forward control design.
​
In the BLENDAIRE II system has a feedback loop also included as standard. It performs a final check to ensure the gas quality is as desired. Any discrepancy detected is sent back to the feed forward control loop for an overall compensation of ALL errors associated with the measuring instruments and the assumed CV of LPG. The problem of conventional mixing systems using feedback control alone is most obvious at start-up and under low flow conditions. None can deliver an accurate mix immediately upon start-up.
When an off-ratio signal is received by the calorimeter, the control system will try to make adjustments to eliminate this error. However, due to the time lag of the signal the correction will not be appropriate for the time being and hence may even amplify the error! It requires a long time for the system to stabilize close to the setpoint and oscillations may continue due to the phased out feedback signals. Under very low flow, regulators for air and/or LPG tend to keep opening and closing all the time, with intermittent spurts of gas injecting into the downstream. Such conditions cause an imbalance of pressures between the two and result in an unstable mix with the potential of generating a hazardous mixture.
In the BLENDAIRE II, the flow signal of LPG is sent to the PLC which then issues a command for the air flow control valve to act – before mixing takes place. The signals occur instantaneously. Upon receiving a signal, the valve is first positioned in accordance with the flow coefficient, which is defined as the relationship between the valve position and the flowrate based on the current differential pressure across the valve. The actual air flowrate measured by the flow meter is then compared with the required flowrate and necessary fine adjustments to the control valve position are made automatically.
The initial response of the valve is direct-acting and takes into account of the momentary unbalanced downstream pressure at startup. It ensures that the valve is set to the approximate position immediately upon start-up, without having to wait for any feedback signal or a long process of back and forth adjustments as is typically the case required in conventional blenders. The subsequent fine adjustment from this position is fast and accurate. The fast and accurate response of the BLENDAIRE II from startup facilitates the automation of the load tracking process In BLENDAIRE II systems parameters (including pressure and/or flowrate) can be set to shut off the mixed gas outlet valve and reopen it at a lower downstream pressure all automatically, eliminating the concern of turndown ratio. This option is called LINE-PAK™.

DOWNLOADS
​
ExVeritas ATEX Certificate
​
​
Safety Features
Due to the extreme simplicity of the system, chance of mechanical failure is virtually nil. There are only three moving components in the BLENDAIRE II – two flow meters and one air flow control valve. It is designed to be fail-safe with TEN elements of protection incorporated. The mixed gas outlet valve will be shut off immediately upon any of the following circumstances:​
​
-
If the LPG flow meter fails to move or send out signals
-
If the air flow meter fails to move or send out signals
-
If there is a substantial discrepancy between the actual and required air flowrate, as it may indicate the malfunction of the air flow meter or control valve
-
If there is a substantial discrepancy between the air pressure downstream of the control valve and the mixed gas as it may also indicate the malfunction of the control valve
-
If the air flow control valve fails to receive a signal or move according to the signal(s) received
-
If any of the pressure and temperature transmitters for LPG and air fails to transmit signals to the PLC
-
Low LPG temperature, and high/low LPG/air pressure, etc. are normally safeguarded up stream of the blender, but even if it happens it will not affect the safe operation of the BLENDAIRE II system at all as long as there is no condensation of LPG within the system. If desired limits may be set to shut off the mixed gas outlet valve as well.
-
If the gas quality deviates from the setpoint exceeding a preset limit for ANY REASON
-
-
Any channel in the input and output module of the PLC fails
​
-
The CPU of the PLC fails After the mixed gas outlet valve is shut, an alarm with an easy-to-understand message in English or an alternate language is issued for quick identification of the problem. The outlet valve can be reopened after the problem has been rectified. Optionally a software warn standby or hardware hot standby system for the CPU can be added. In case the active CPU fails all its duties will be automatically transferred to the standby one. The transfer is transparent to the user as there will be no interruption of the process or loss of any data.
Advantages of the BLENDAIRE II System
​​
-
Fail-safe design with many safety features included
-
Informative alarm messages (with optional logging function) for quick identification of faults
-
Simplicity in construction minimizing the chance of mechanical failure
-
High confidence of reliability as all major components used are standard and matured products made by reputable manufacturers, hence
-
Proven reliability
-
In general, very short delivery lead-time
-
Replacement components and parts are readily available on the market at reasonable price
-
Fast response and very accurate blending with both feed forward and feedback control
-
Very wide range of mixing ratio easily adjustable without modification to the hardware configuration
-
Smooth start-up and operation for maintaining consistent gas quality at all times
-
Turndown ratio is the same as the LPG and/or air flow meters, which is typically 40 to 1 or better
-
Automatic load tracking at low loads (optional) making turndown ratio no longer a concern. The mixed gas outlet valve will be set to shut off above a certain pressure or below a certain flow rate, and re-start at a lower pressure, all automatically
-
Only clean air will pass through the control valve, hence there will be no blockage of orifice or sticking of moving mechanism by impurities in LPG, or the need to clean them at regular intervals
-
Low LPG pressure required – the same as required for mixed gas, making it possible to vaporize LPG at lower temperatures to avoid formation of polymers from unsaturated hydrocarbons. There will be less need to run the LPG stabilizing pump, meaning less wear and tear and less energy consumption
-
Low compressed air pressure required, meaning less energy consumption and longer motor life
-
Changing the mixed gas pressure is as simple as changing the outlet pressure of the LPG regulator
-
Dual streams can be mounted in a single skid with only one LPG and air inlet and one mixed gas outlet for simpler installation
-
One integrated control panel for multiple stream blenders
-
Industrial standard Profibus DP communications capability for easy integration with the central control system; other communication options are also available
-
High capacity per stream means lower equipment and installation cost
-
Total corrected and uncorrected flow information available from the two meters without the need of an additional total flow meter – a substantial saving in the total system cost
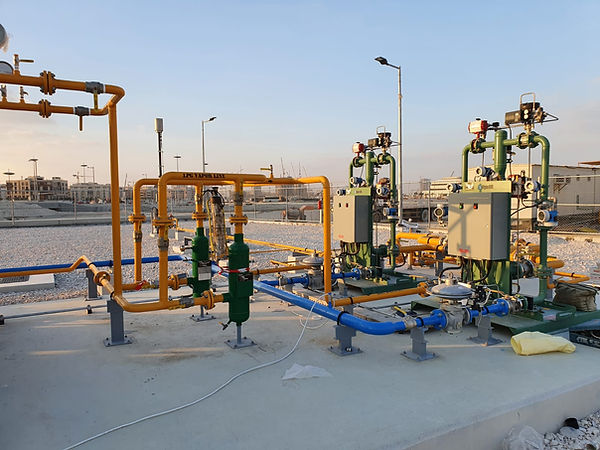.jpg)
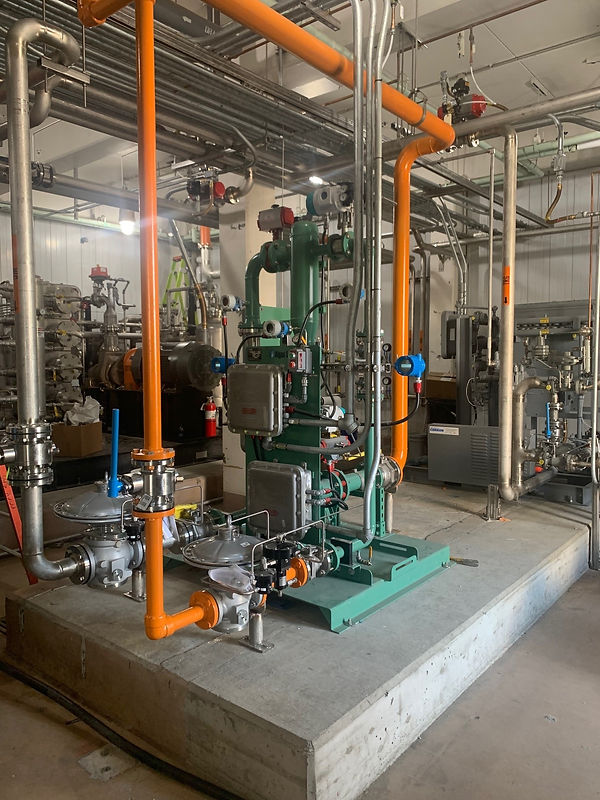